Technical Information
Swiftcrete concrete blankets are the result of extensive research, development, precision manufacturing and advanced technology.
About Swiftcrete Concrete Blankets/Rolls
Flexible concrete blankets (FCB), also known as cement blankets or flexible concrete rolls, are cement-based polymer composite material blankets, often abbreviated as GCCM. This innovative material seamlessly blends concrete with fibre components. Concrete blankets are stored in rolls and are highly flexible until they are ready for use.
Upon exposure to water through a simple spraying process, the FCB hydrates and solidifies into a robust structure resembling cast-in-place concrete. It boasts exceptional strength and durability.
The application of the concrete blanket is straightforward. It involves unrolling, laying, cutting and securing, followed by water hydration.
The flexible concrete blankets/rolls are comprised of a combination of essential materials, including fibrous structural components, specifically formulated dry concrete powders developed with proprietary rights, both organic and inorganic reinforcing fibres and layers for controlling water penetration.
The inclusion of reinforcing fibres enhances the toughness of the blanket, preventing cracks and ensuring the overall structure’s integrity.
Properties of Flexible Concrete Blankets
High Strength
Our concrete blankets are made from a unique concrete formula that achieves compression strength values of up to 65MPa, and a flexural strength of up to 20MPa. The inclusion of reinforcing fibres enhances the structure’s overall strength and stability.
Durable
The strength and toughness of hardened concrete blankets are remarkable. Once hardened, the product demonstrates resistance to ageing, corrosion, and freeze-thaw cycles, ensuring a service life of up to 50 years.
Flexible
During application, the concrete blankets can be easily bent to conform to the terrain’s contours. Prior to hydration, the concrete blankets can be cut using a utility knife or an electric cloth cutter, allowing for adaptability to various construction scenarios.

Years Established
Annual Production
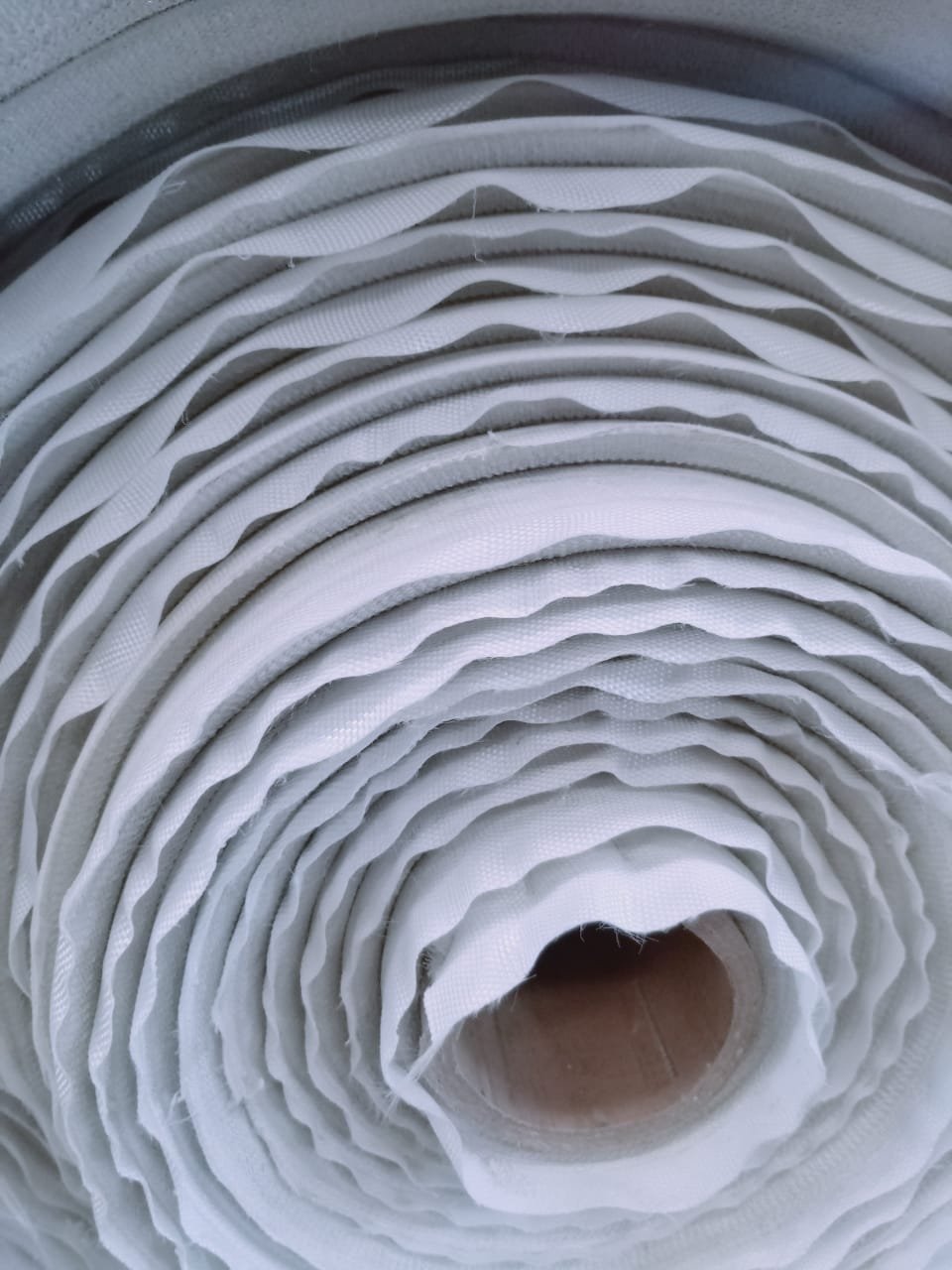
Product Parameters
The regular size for Swiftcrete concrete rolls is 2m wide by 50m long. There are however several variations available in terms of thickness, density and hydration time, depending on your requirements. The maximum customisable width is 2.4m. The table below illustrates the available combinations.
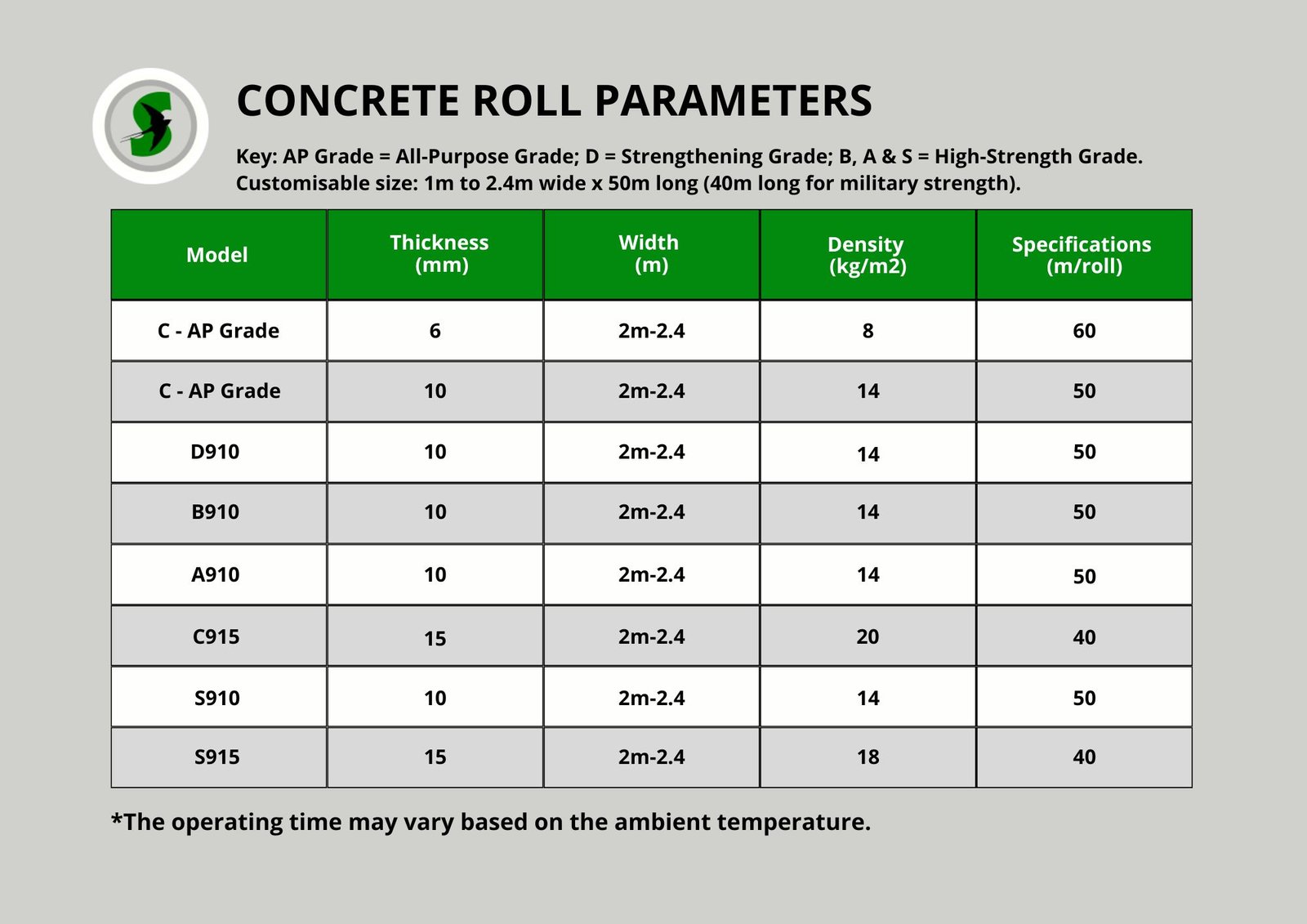
Product Testing

Testing Standard: GB/TI346-2011
C/B series products:
* 3-day strength achieves 40MPa
* 3-day strength reaches 80% of 28-day strength.
S series products:
* 3-hour strength achieves 40MPa
* later strength continues to increase.
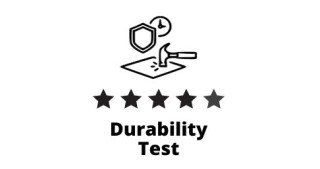
Wear resistance: tested according to DIN52108, where achieving <0.1g/cm2 is equivalent to half the wear resistance of C40 concrete.
Freeze/thaw cycle resistance: assessed using ASTM C1185, with a requirement of passing 200 cycles, following the performance criteria of GCT 412 2006 Fiber Cement Board.
Water resistance: evaluated through ASTM D-6460, which determines the suitability of the material for erosion control in rainwater channels.
Fire resistance: tested against GB 8624-2012, with a classification of Grade A, indicating high combustion performance for building materials and products.
UV ageing test: conforms to ASTMM D4355, which involves subjecting the material to 500 hours of UV ageing while retaining more than 95% of its strength.
Acid and alkali resistance test: conducted in a pH range of 3-13 to assess the material’s resistance to acidic and alkaline environments.
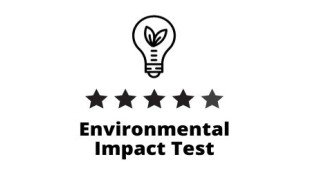
Solid waste leaching toxicity test (US EPA TCLP test: conforms to HJ/T299-2007, which is the equivalent of the US EPA TCLP (Toxicity Characteristic Leaching Procedure) test. The material’s leaching toxicity is assessed to ensure that it falls below the specified standard values.
pH test after hydration reaction: the material exhibits a pH of 7.5 before hydration and a pH value of 8.3 after undergoing the hydration reaction.
Common Usage
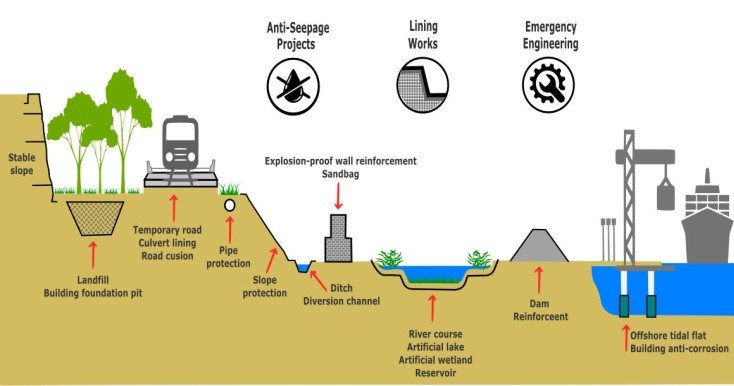
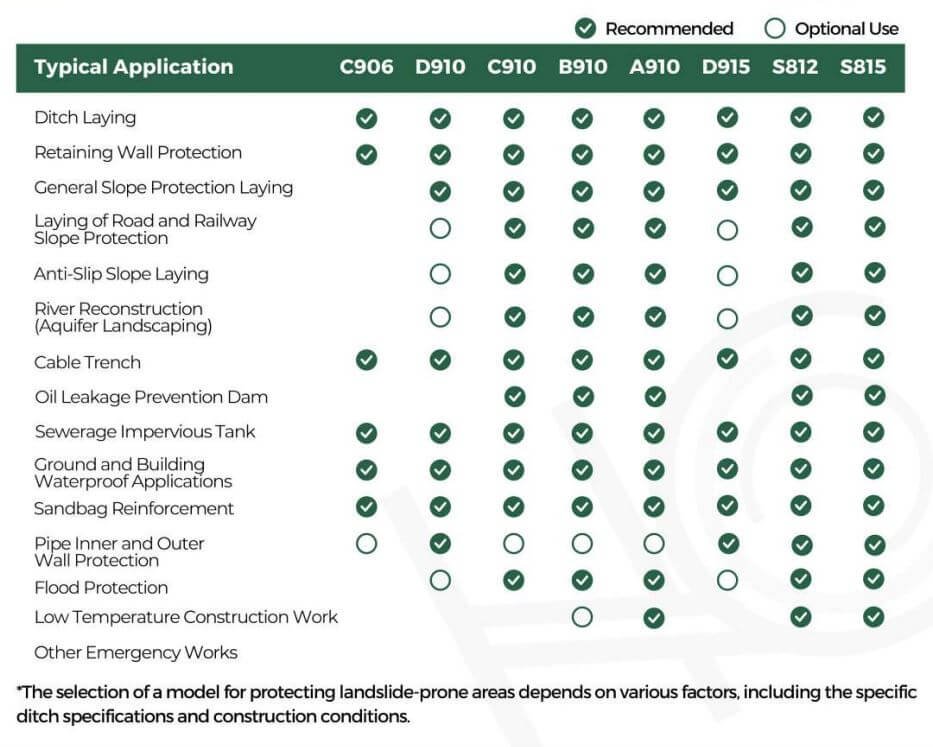
Use Environment
For the best results, Swiftcrete concrete blankets should be used in temperatures above 5 degrees Celcius. In cases of extreme high or low temperatures, it is advisable to request advice from the manufacturer’s technical team.
For S series products, construction can be undertaken in winter. However, when applying this product in specialised environments, such as industrial sewerage settings, a thorough evaluation is necessary.
Water Hardening Method
Once Swiftcrete concrete blankets have been laid in their designated positions, water is added to initiate the hardening process. The optimal water-to-concrete blanket weight ratio is 1:2.
Once the product has hardened, a further spraying of water will cure it. At this stage, the water volume does not need to be precisely controlled. In the case of underwater construction, it is possible to work with the product while directly immersed in water.
There are no specific water quality requirements – even seawater can be used for hydration. It is, however, essential to ensure that the water used is free of any oil contaminants.
APPLICATION ADVICE
Ditches
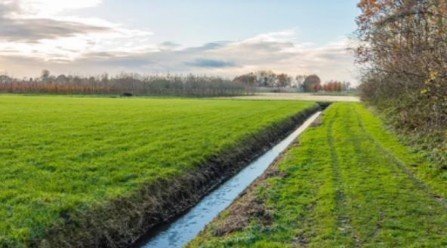
Scope of Application
- Water conservancy projects
- Agricultural ditches
- Ecological ditches
- Rain ditches
- Mountain ditches
- Highway drainage ditches
- Temporary diversion ditches
- Sewerage ditches
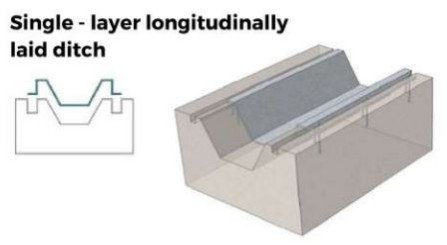
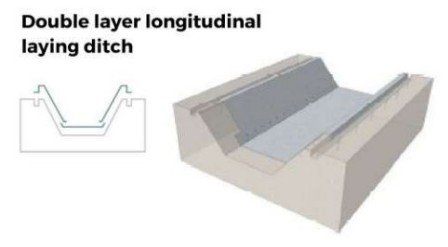
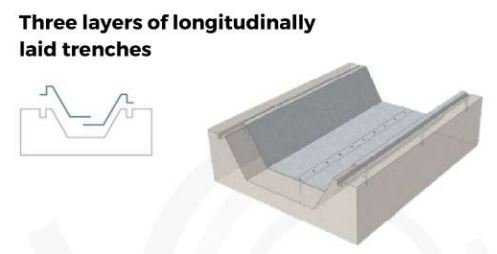
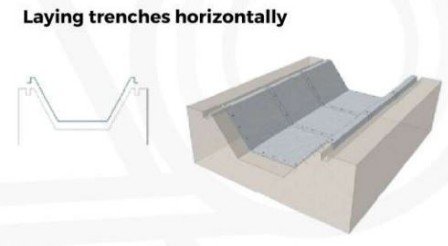
Engineering Advantages
Exceptional construction efficiency: the construction efficiency of Swiftcrete concrete blankets is equivalent to 20 times that of the traditional mortar masonry method. This speeds up the completion of projects significantly.
No special pad compaction: there is no special pad compaction required when laying this material on ditches or slopes, simplifying the installation process.
No mortar mixing required: unlike traditional methods, no mortar mixing is necessary. The product can be installed in wet conditions and environments.
Outstanding frost and weather resistance: the concrete blankets exhibit excellent frost and weather resistance, ensuring long-lasting performance.
Environmentally friendly: Swiftcrete concrete blankets are environmentally friendly and have a low carbon footprint. This is as a result of significant reductions in sand and gravel requirements.
Simplicity and speed: the installation process is quick and simple, shortening the construction period. It can be used within 24 hours after hydration without the need for repeated maintenance.
Construction Methods
The groove design works best for ditches. Carefully assess the length and width of the trench, choose an appropriate laying technique, and aim to minimise material wastage.
In practice, there are four common laying scenarios to guide the process (see diagrams on the left).
The construction phase should be determined in accordance with the direction of the water flow, paying special attention to the overlapping sections. It is advisable to initiate construction from the downstream end, and gradually progress towards the upstream end.
Typically, lap joint installations involve a 10cm overlap and the choice of overlap method should be determined by the anti-seepage requirements of the project.
For edge treatment, a method involving filling and securing with a drill works best. This necessitates creating a trench at the top of the slope and reinforcing it using a drill. In instances which involve larger trenches, drilling at the bottom corners of the sides is essential.
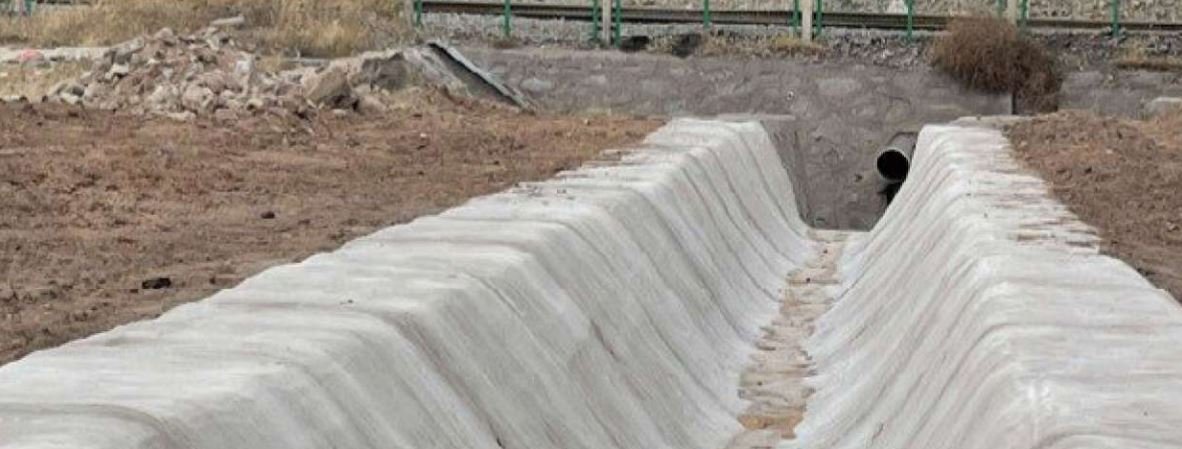
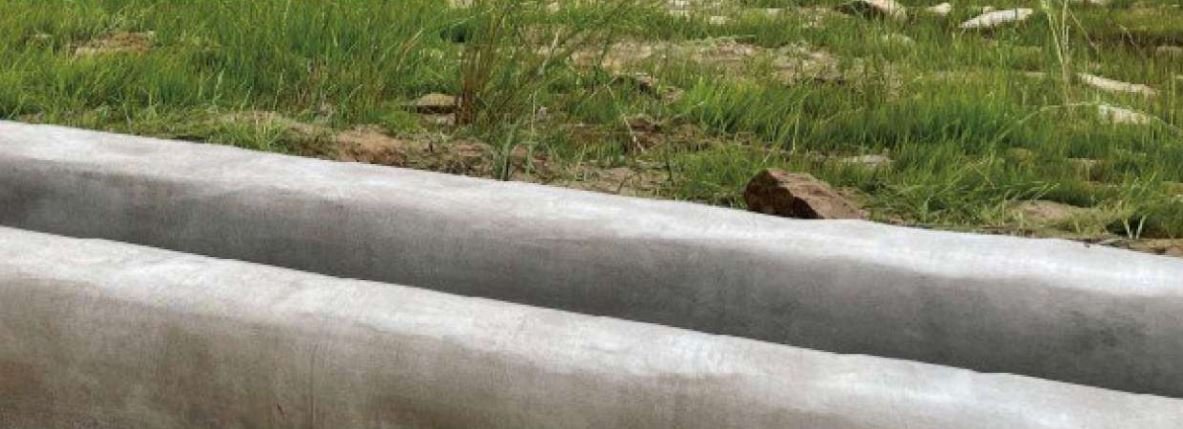
Slopes
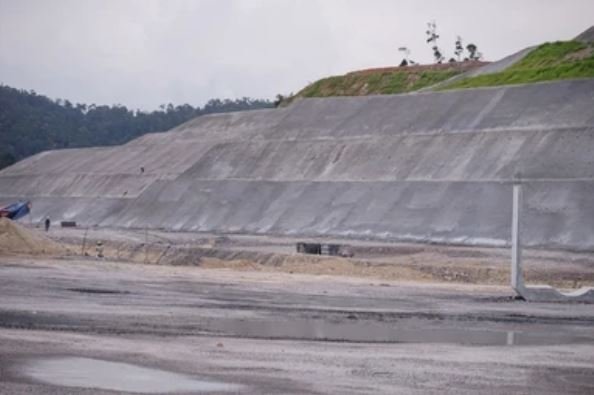
Scope of Application
- Mine slope protection
- Roadside protection
- Building slopes
- Anti-collapse reinforcement
- Drainage ditch laying in mine waste slopes
- Coast and wharf anti-scour measures
- Embankment protection
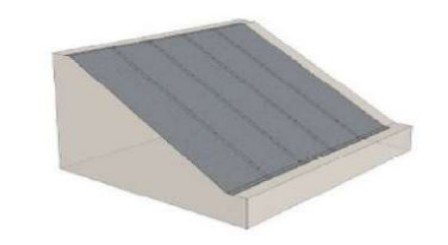
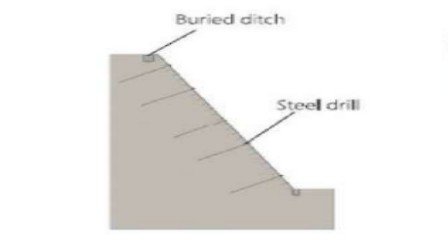
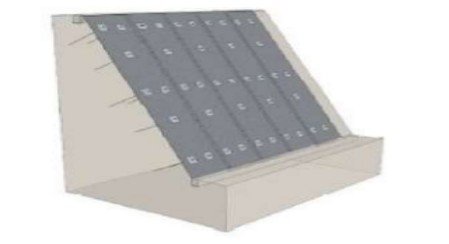
Concrete Blanket Advantages
Versatile on any slope: the product is adaptable to any slope ratio, making it a versatile solution for a wide range of terrain and landscape requirements.
Landslide prevention: the concrete blankets prevent any landslides, offering reliable erosion control and slope stabilisation. This provides an effective safeguard against natural disasters.
Superior mechanical properties: compared to traditional mortar-spraying methods, our concrete blankets boast significantly higher mechanical properties and durability, ensuring long-lasting and robust performance in a variety of applications.
Construction Method
Technical Points of Slope Protection
For slope protection, determine the concrete blanket’s construction length based on slope dimensions. Cut accordingly.
Begin installation from the top, proceeding down the slope.
When adding an additional piece of concrete blanket, ensure that it properly overlaps the first piece and secure the connections with screws.
Technical Points of Special Slope Protection
Slopes that are vulnerable to landslides, steep slopes, or slopes with non-uniform geological structures can present unique challenges.
To reinforce these types of specialised slopes, extra protection measures need to be implemented. This involves filling the slope’s edges and anchoring them with steel brazing.
To start, dig a 250mm x 250mm landfill ditch, fix the concrete at the base of the landfill ditch with anchor rods, and complete with backfilling.
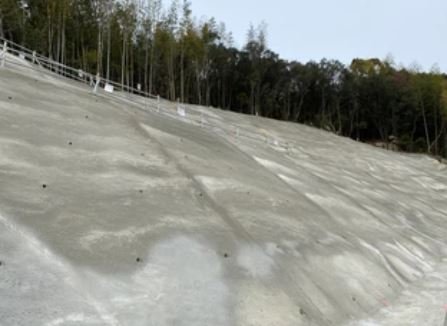
Pools
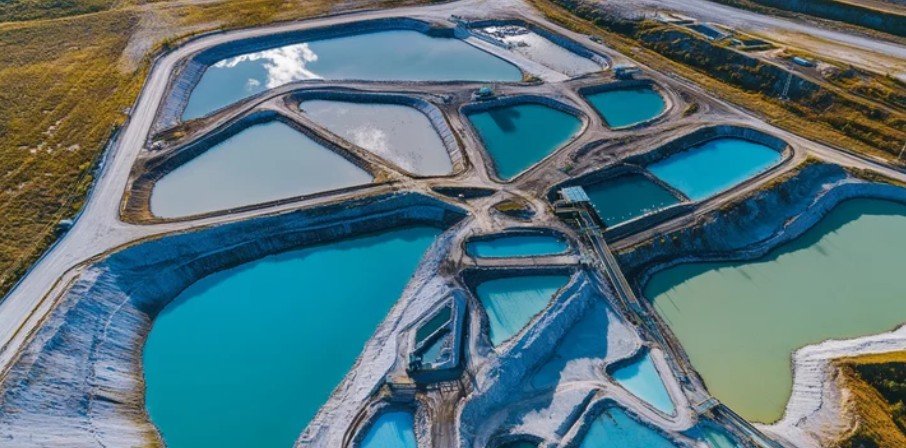
Scope of Application
- Cisterns and reservoirs
- Washing pools
- Property sewerage reservoirs
- Sewage treatment plants
- Swirl sand settling
- Haikou pumping station sumps
- Anti-seepage liners for fish ponds
- Reinforcement of embankments
- Protection against erosion in mariculture
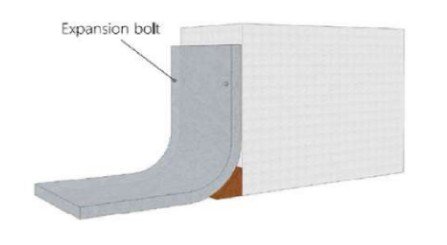
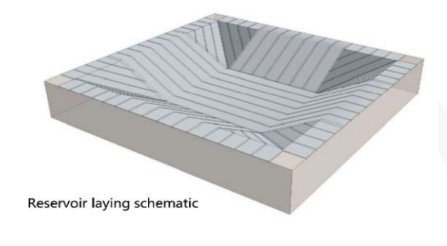
Concrete Blanket Advantages
- Corrosion and erosion resistance
- Anti-freeze, anti-thaw, anti-ageing, anti-ultraviolet
- Suitable for use in environments with a pH value of 3 – 12
- Contains no volatile substances
- Features a structural bow
- Utilises hot-melt welding for superior anti-seepage performance
- Effectively prevents weeds from damaging the embankment
Construction Method
Depending on the size of the pool, a combination of vertical and horizontal laying methods are used, taking advantage of the material’s flexibility to cover corners and match any pond contour precisely.
In areas that are prone to corrosion and susceptible to scour, the flexible concrete blankets are anchored securely to concrete bases using adhesive and anti-bolts. This ensures their stability and effectiveness in providing erosion control and protection.
This product is designed to be used in water environments, making it suitable for applications that require contact with water, such as pool or aquatic-setting installations.
When laying the concrete blanket along the shoreline, it can be affixed either directly using a drill, or in conjunction with edge filling or drilling.
To maintain structural integrity and stability, it is advisable to excavate a joint trench, typically measuring around 250mm x 250mm, for subsequent backfilling.
In landfill applications, the choice of corrosion-resistant hardware or fasteners should be made based on the specific situation and requirements. This will ensure long-term durability and reliable performance which is tailored to the environmental conditions.
Technical Points on Pool Wall Construction
For wall connections, use expansion bolts and select fasteners based on the specific requirements, considering factors like fire or corrosion resistance.